Our house has a roof angle of around 22 degrees. Standard heat recovery system pipework comes with 45 degree or 90 degree bends so something flexible was needed to join vertical runs coming off the top of the heat recovery unit that go across the top of the house by passing through the rafter space. These runs have to be made with insulated pipe because as the pipe goes into a cold space above the sheepswool insulation there is a risk of condensation if the air has sufficient moisture in it.
So on our last visit to CVC (www.cvcdirect.co.uk) we got a short length of flexible Aluminium ducting, some worm drive clips and some bubblewrap and aluminium foil insulating sleeve and assembled it, using the foil tape to secure the outer insulation. Here’s one we prepared earlier.
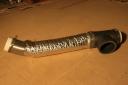
This then slid into position a treat and bends nicely to fit into the busy space between the rafters. The Aluminium pipe needs a white plastic connector on the end to enable it to fit into the 125mm white plastic pipe coming up from the Heat Recovery Unit.
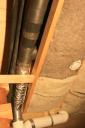
The giant worm drive clips supplied are really easy to use compared to a conventional clip of this sort.
They have a hinging screw, so in a confined space you don’t have to spend ages doing them up, just close the clip as much as you can by hand, swing the hinging screw into position to engage the pierced stainless steel band on the screw thread and tighten the last bit with a screw driver.
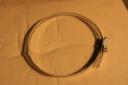